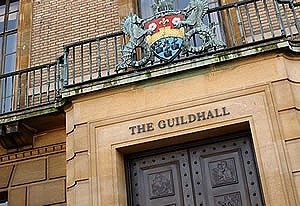
The Guildhall, Cambridge
The Guildhall in Cambridge, an Interesting and Unusual Alarm Upgrade
Not all electrical installation contracts are straight forward and not all alarm upgrades are all about the alarm!
The Guildhall in Cambridge, a very prestigious place, had to have its fire alarm system upgraded to comply with L2 requirements of BS5839. Whilst the upgrade itself, from a technical perspective, was no issue the logistics and the need to keep disruption to a minimum were very important.
As The Guildhall is a listed building and occupied by over 150 members of staff there were many restrictions and considerations.
By working in close partnership with Cambridge City Council and the Building Control Officer, we were able to comply with the restrictions associated with the listed status of the building and maintain its integrity totally.
The construction of the building necessitated drilling in certain areas and due consideration had to be taken to ensure the noise from the drilling was limited to certain times of the day in order to work around important Council meetings and functions being held in the Guildhall. The Mayor’s Chambers and offices are also located within the Guildhall, another disruption consideration to factor in.
By completing a schedule of works and sticking to it, our engineers were able to successfully complete the alarm upgrade and ensure everyone was kept happy.
A strange quirk of the Guildhall is that the heating system and pipework is located within the concrete ceilings. So, before any drilling was carried out, a hi tech metal detector was used to locate the pipework so as to prevent any water leaks occurring.
Although the contract lasted several months the project was completed to the full satisfaction of Cambridge City Council without a single complaint from staff or any damage or leaks to the heating pipe work.
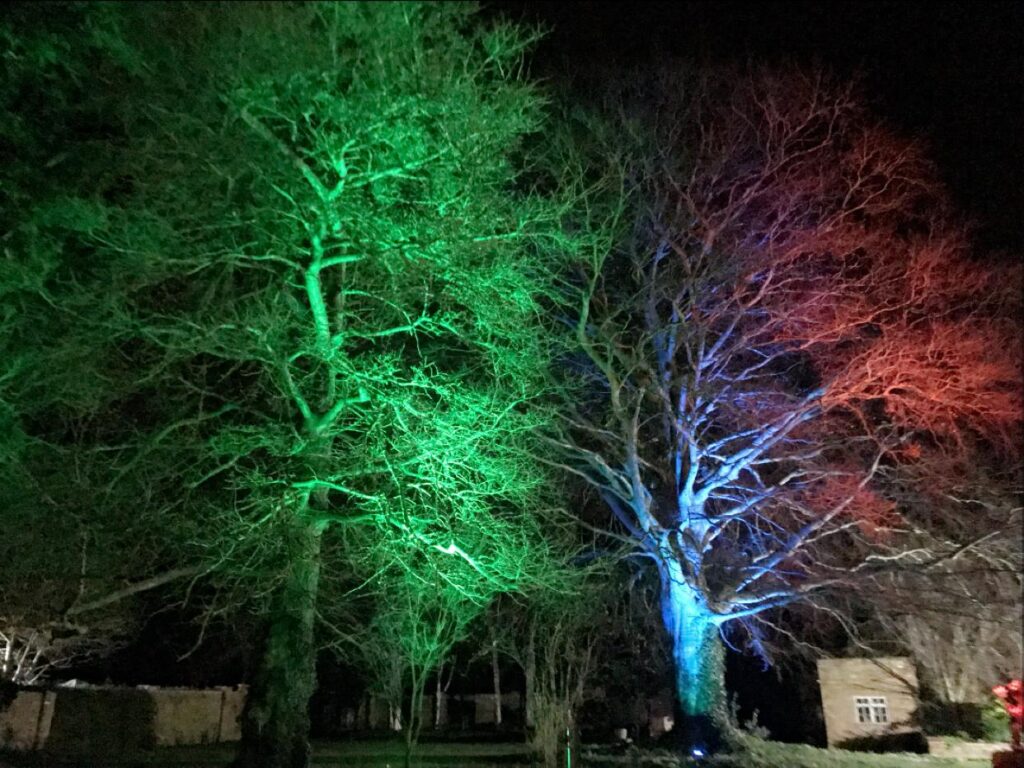
Dixon International
Outdoor Lighting for Company HQ’s Gardens
It’s been said that when you have something to shout about, it should be put up in lights. Dixon International Groups Headquarters near Cambridge are a perfect example.
The stunning location and beautiful surroundings were crying out to be lit up. They wanted a bright, colourful and energy efficient display. So, FCE were called in to design and provide the ideal solution for their gardens.
The results are well worth looking at.
“Dixon International Group have used the services of FCE for many years, they are always very responsive when we need them in a hurry to get a machine back up and running. They’re reliable and can do all the different kind of electrical work we need such as the fire alarms, machine and buildings maintenance and repairs and installations. It makes life easier to deal with one company, the pricing is right and we can trust them to do a good job every time. I would be happy to put my name to anything recommending FCE Ltd.”
David Allen, Works Manager, Dixon International Group Ltd
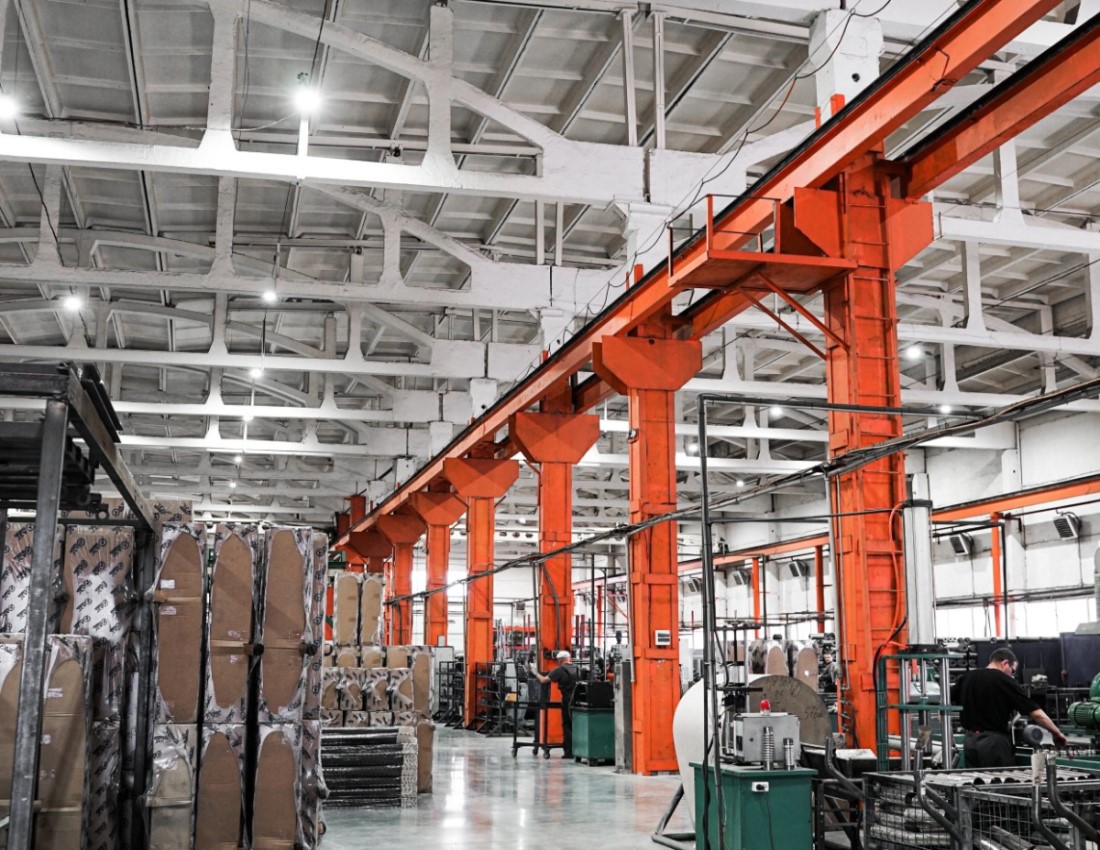
A1 Steel , Peterborough
Superior LED Lighting, 89% Saving on Energy Costs and an Interest Free Loan to Pay for it.
“It has been a true win, win situation; I am saving money, reducing CO2 emissions, and have provided a better working environment for my employees.”
Dean Johnson, Managing Director, A1 Steel Ltd
As a growing, successful company, A1 Steel Ltd needed to re-locate to larger premises and they contracted FCE Ltd to provide new lighting and power for their new offices.
The specialist lighting team at FCE recommended the use of energy efficient lighting in the sales office with presence detection lighting to the toilets, corridors and the board room. The rationale behind this recommendation was that it would ensure that all A1 Steel’s employees benefitted from an optimum, well lit, working environment that would also reduce lighting costs and keep them to a minimum.
A lighting survey of the welding and fabrication workshop was also conducted, which highlighted that the existing lighting, comprising of a mixture of 42 metal halide and fluorescent strip fittings consumed 34,495 KW/hr per annum at a cost of £3,449.51 but only provided a maximum lighting level of 90 lux. It was proven that the cost was far from economical and could be dramatically improved as could the quality of the lighting.
Using our 3D lighting design software we calculated and designed a system that would give far better lighting conditions and massive savings year on year. The installation of 21x T5 energy efficient fluorescent light fittings was recommended and, in order to maximize energy savings, it was also recommended that built-in presence detection and daylight sensors were fitted.
The presence detection sensors ensure that, when unoccupied, the lights would automatically dim to 10% output, however, when presence was detected they would immediately power up to 100% output.
In conjunction with daylight sensors monitoring natural daylight from skylights and windows and adjusting power accordingly, a constant and optimal working light level was maintained whilst taking advantage of free light sources to maximise energy savings.
The annual running costs of this new lighting setup were calculated at £365.00 providing an energy saving in excess of 89% a huge saving of £3,084.51 every year. In addition to the savings, the maximum lighting levels would be increased by over 400% to 385 lux. Furthermore, a staggering 16.4 tonnes of CO2 emissions would also be saved per annum.
Although the cost savings would be paid back in less than 3 years, FCE were also able to arrange, and have approved, a 100% interest free loan from the Government funded ‘Carbon Trust’.
The loan repayments were over three years, meaning that the new lighting installation was self funded by the energy savings it produced. Importantly, in year four and thereafter, the lower costs could drop straight to the bottom line as increased profit.